Plywood tearout is a prevalent issue in the world of woodworking, characterized by the unintended tearing or splintering of wood fibers during cutting or routing operations. This problematic occurrence can severely detract from plywood surfaces’ overall aesthetic appeal and structural integrity, rendering them less appealing and potentially compromising their strength.
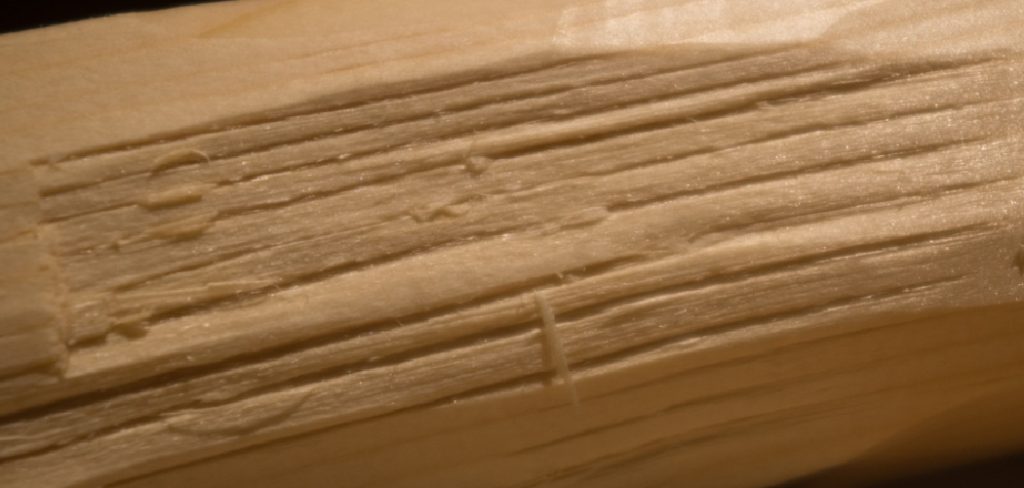
Understanding how to fix plywood tearout is crucial for amateur and professional woodworkers alike, as it ensures that the final product looks polished and professional and maintains its durability and functional integrity. This guide is designed to walk you through a comprehensive, step-by-step approach to repairing plywood tearout effectively, covering everything from assessing the extent of the damage to applying the finishing touches that bring the surface back to its original condition or even better.
Assessing the Damage
A. Identifying Tearout Areas:
The initial step in fixing plywood tearout involves carefully inspecting the plywood surface to locate tearout damage. This necessitates a thorough examination to determine the location, size, and severity of the damage. A bright light can help highlight these areas, revealing even minor splinters or tears that might be overlooked. It’s crucial to mark these spots with a pencil or painter’s tape to ensure they are all addressed during the repair process.
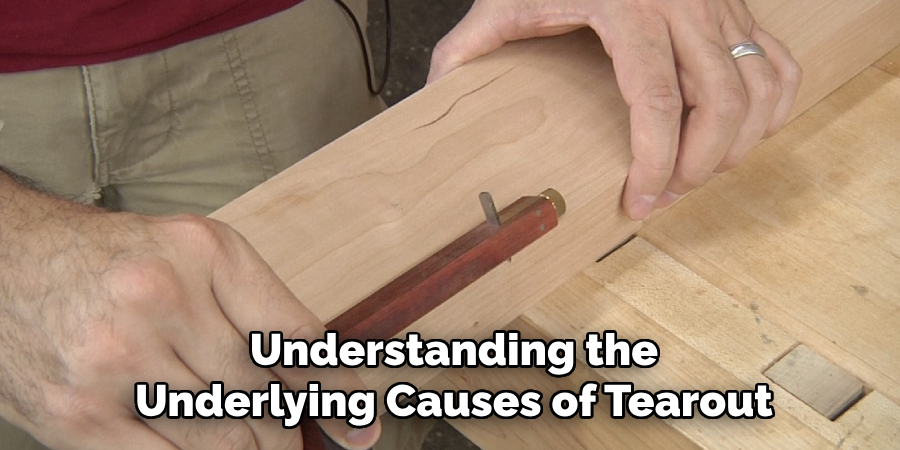
B. Understanding Tearout Causes:
Understanding the underlying causes of tearout can be instrumental in both repairing the damage and preventing future occurrences. Several factors contribute to plywood tearout, including the speed at which the material is cut, the cutting blade’s sharpness, and the wood grain’s orientation. For instance, a dull blade tends to tear the wood fibers rather than cut cleanly through them, while cutting too quickly can exacerbate this effect. Similarly, cutting against the grain increases the likelihood of tearout. Recognizing these factors can guide both the repair method chosen and adjustments in future cutting techniques.
C. Considering Repair Options:
The tearout’s severity, the plywood surface’s desired finish, and the final appearance all play pivotal roles in determining the most suitable repair strategy. For slight to moderate tearout, wood filler or putty might suffice, while more severe damage may necessitate creating and installing patch pieces from matching plywood. The choice between these options depends on whether the goal is merely structural repair or if restoring visual appeal is also a priority. When the aesthetic outcome is critical, more time-consuming and detailed repairs might be required to achieve a seamless finish.
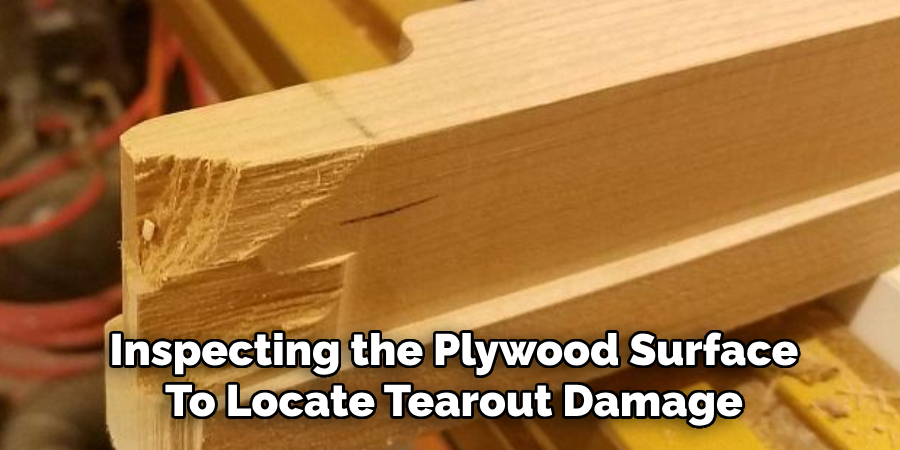
How to Fix Plywood Tearout: Filling and Patching
A. Using Wood Filler:
One of the initial steps in addressing minor plywood tearout is the application of wood filler or putty. This method is particularly suitable for small, superficial damages where the structural integrity of the plywood is largely unaffected. Begin by choosing a wood filler that closely matches the color of your plywood. Apply the filler directly into the tearout areas, pressing it firmly to ensure it fills the gaps entirely. Using a putty knife, level the filler with the surface of the plywood, scraping away any excess material. Allow the filler to dry as per the manufacturer’s instructions before proceeding to sand the area smoothly, integrating the repair seamlessly with the rest of the surface.
B. Creating Patch Pieces:
For larger tearout areas or where the damage extends deeper into the plywood, creating and installing patch pieces from scrap plywood or matching wood stock can provide a more refined and durable repair. Begin by accurately measuring the dimensions of the tearout area and cutting a piece of plywood or wood that matches the thickness and grain pattern of the original surface. Precise cutting is essential here to ensure the patch piece fits snugly, without gaps.
C. Gluing and Securing Patches:
Once the patch piece is ready, apply sufficient wood glue to its edges and the corresponding area on the plywood. Carefully place the patch into the tearout area, pressing it firmly to ensure a strong bond.
Use clamps or place heavy weights over the patch to maintain pressure while the glue sets. This will prevent the patch from shifting or rising, ensuring it remains flush with the surrounding surface. After the glue has fully cured—a process that can take several hours or, according to the glue manufacturer’s instructions—remove the clamps or weights. You may then proceed to sand the area lightly, blending the patch’s edges seamlessly into the original plywood surface, making the repair virtually invisible.
How to Fix Plywood Tearout: Sanding and Smoothing
A. Sanding Surface Flush
Achieving a flawless finish on repaired plywood surfaces demands meticulous sanding to ensure that filled or patched areas are perfectly flush with the surrounding surface. Start with medium-grit sandpaper to remove the bulk of the excess filler or to level the patch piece efficiently. Gradually shift to fine-grit sandpaper, ideally around 220 to 320 grit, for the final smoothing. Employ smooth, even strokes in the direction of the grain to avoid creating additional scratches or blemishes on the plywood surface. This careful progression from coarser to finer grits will help you achieve a smooth, uniform surface without compromising the integrity or appearance of the plywood.
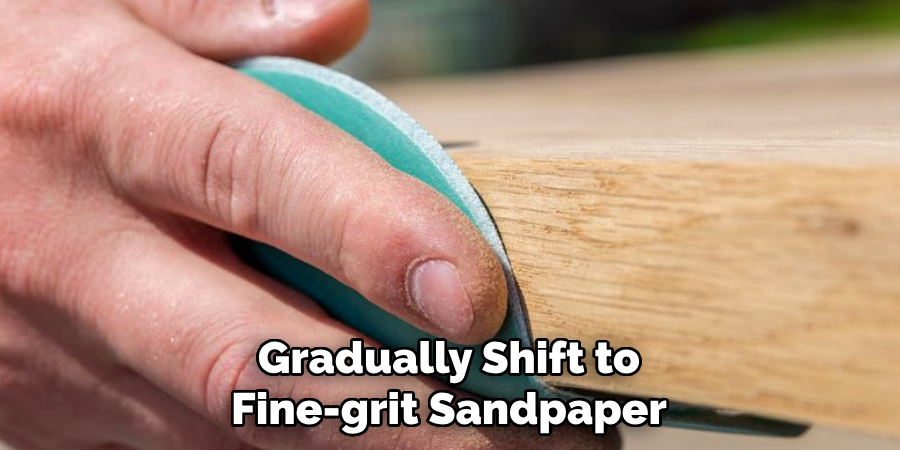
B. Blending Edges
The secret to an invisible repair lies in seamlessly blending the edges of filled or patched areas with the surrounding plywood surface. After sanding the repaired area flush, lightly sand the perimeter of the repair to feather the edges into the existing surface. This blending process helps eliminate any visible transitions between the repaired section and the rest of the plywood. A higher-grit sandpaper, such as 400 grit, can be effective for this final blending step, ensuring a smooth transition that is undetectable both visually and to the touch.
C. Checking for Smoothness
The final step in the sanding and smoothing process involves thoroughly inspecting the repaired areas for smoothness and consistency. Gently run your fingers or a soft cloth over the surface to feel for any irregularities, bumps, or remaining rough patches. This tactile inspection is critical, as even the smallest imperfection can appear once a finish is applied.
Pay particular attention to the areas where the repair meets the original plywood. Any discrepancies in texture or level should be addressed with additional fine sanding until the entire surface feels uniform. Achieving a smooth, consistent surface texture is indispensable for a professional-quality finish, ensuring the repaired plywood is visually appealing and feels impeccable to the touch.
Sealing and Finishing
A. Applying Wood Sealer
Once the sanding and smoothing process is complete and you are satisfied with the uniformity and texture of the repaired plywood surface, applying a wood sealer or primer is the next crucial step. This protective layer is vital for sealing the porous surface of the wood filler or the new patch, effectively blocking moisture, preventing stains, and safeguarding against further damage.
Select a sealer that is compatible with both the type of plywood and the final finish you intend to apply. Using a clean brush or a roller, apply the sealer evenly across the entire surface, paying extra attention to the repaired areas to ensure they are thoroughly coated. Allow the sealer to penetrate and set according to the manufacturer’s instructions, which can vary but generally involve a drying time of at least a few hours.
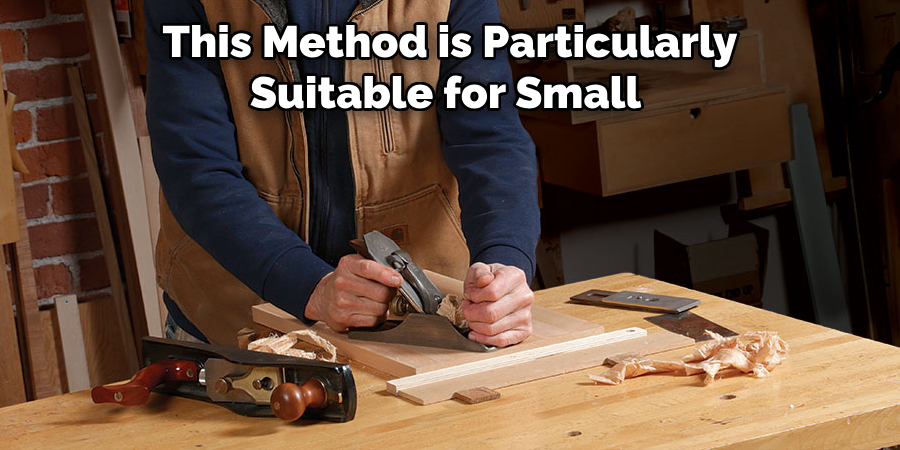
B. Matching Surface Finish
Achieving a matching surface finish or paint color is fundamental to the aesthetic integration of the repair with the surrounding plywood surface. If the original plywood is painted or has a particular finish, you must replicate this as closely as possible. This might involve mixing paints or stains to match the existing color and sheen. Sometimes, consulting with a paint specialist can provide the best match.
After the sealer has dried, apply the finish or paint using steady, even strokes to avoid drips or inconsistencies. If you’re working with stain, apply with a rag or brush, wiping away excess to achieve the desired depth of color. It may require several coats to achieve full coverage for painted surfaces, allowing adequate drying time between each coat as recommended.
C. Allowing Drying Time
The importance of allowing adequate drying time for the sealer and finish cannot be overstated. Rushing this process can lead to various problems, from a finish that peels or chips easily to moisture trapped beneath the surface that could compromise the repair. Adhere strictly to the drying times specified by the products’ manufacturers.
This will vary depending on the type of sealer, paint, or stain, as well as ambient temperature and humidity levels. Only after the final coat has completely dried, which may take up to 24 hours or longer, should the plywood surface be subjected to use or further treatment. This patience ensures the longevity and durability of the repair, contributing to a seamless, professional-quality finish.
Prevention Tips
Preventative measures are key to maintaining the integrity of plywood during woodworking projects, helping to avoid common issues like tearout, splintering, and uneven cuts. Here are some essential tips to ensure clean, professional-quality work every time:
A. Using Sharp Blades
The importance of using sharp blades for cutting tools, such as saws and routers, cannot be overstated. Dull blades are one of the primary culprits of tearout—a condition where the wood is inadvertently ripped or chipped out during the cutting process. Sharp blades make cleaner, smoother cuts by slicing through the wood fibers instead of tearing them. This not only enhances the quality of the cut but also significantly reduces the chances of damaging the plywood. Regularly inspect and sharpen your blades or replace them as needed to maintain optimal performance.
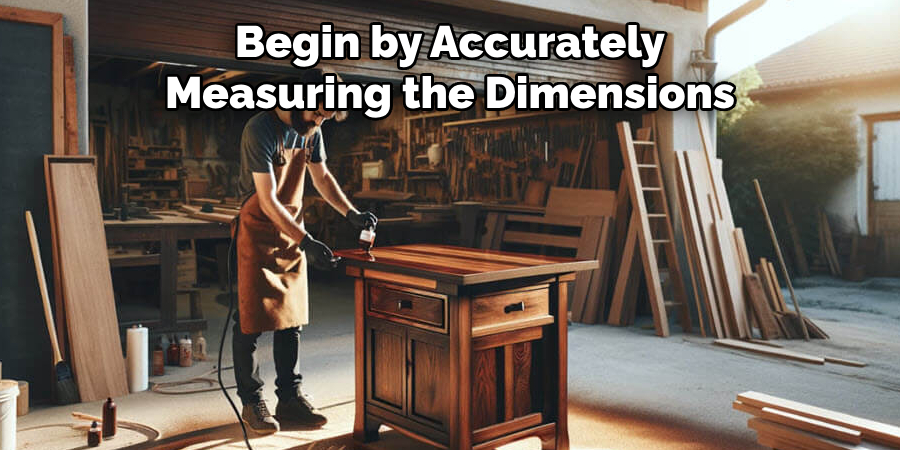
B. Adjusting Cutting Speed
Adjusting the cutting speed and feed rate according to the type of wood you work with is crucial for preventing tearout and ensuring a precise cut. Due to their dense nature, hardwoods require a slower cutting speed to allow the blade to cut through the material without causing damage. On the other hand, softwoods can be cut at a higher speed since they are less dense and easier to work with. The key is to find a balance that allows the blade to work effectively without putting undue stress on the wood or the tool.
C. Supporting Wood Grain
When cutting or routing plywood, supporting the wood grain is essential to minimize the risk of tearout and splintering. One effective technique is to use backer boards or sacrificial materials placed against the underside of the plywood. These materials act as a support system, providing a clean exit point for the cutting blade and thereby protecting the integrity of the plywood’s surface.
Additionally, when routing, always move the tool in the direction opposite to the wood grain to avoid lifting or splintering the fibers. This approach not only preserves the quality of your workpiece but also extends the life of your tools by reducing the resistance they encounter during the cutting process.
Implementing these prevention tips can greatly enhance the quality and appearance of your woodworking projects while also safeguarding your materials and tools. By investing time in proper preparation and technique, you’ll achieve visually pleasing and structurally sound results, with fewer frustrations and corrections along the way.
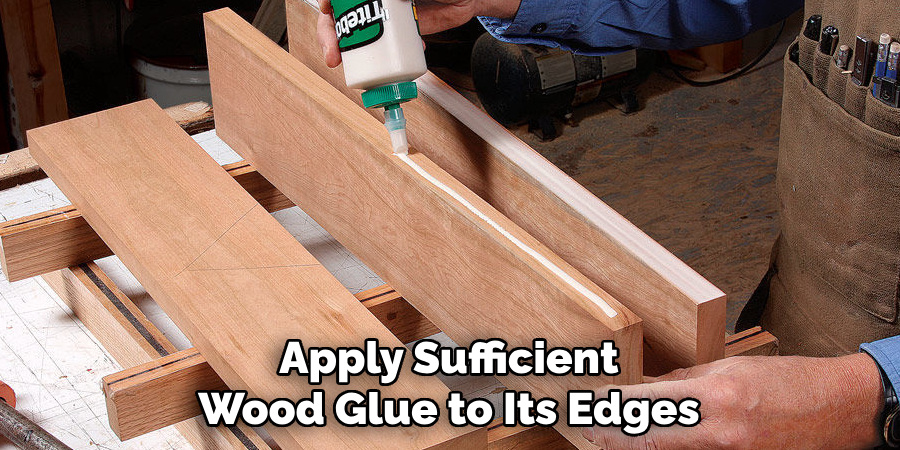
Advanced Repair Techniques
Advanced repair techniques can significantly enhance the appearance and functionality of plywood projects, particularly when dealing with extensive damage or aiming for a flawless finish. Here are three sophisticated methods to consider:
A. Veneer Patching
Veneer patching is an effective method for repairing extensive tearout damage in plywood. This technique involves applying a thin veneer layer over the damaged area, meticulously matching the grain pattern of the existing surface. Select a veneer that closely resembles the plywood in terms of grain pattern and color to achieve a seamless integration. After applying the veneer patch with appropriate adhesive, careful sanding and staining or finishing are necessary to blend the repair with the surrounding area. This method not only conceals the damage but also reinforces the structural integrity of the plywood.
B. Router Inlay
Creating decorative inlays or borders around tearout areas using a router is a creative solution that combines repair with aesthetic enhancement. This involves routing out a predefined section around the damaged area and inserting a piece of matching wood species or a contrasting material such as another type of wood, metal, or even stone. The inlay piece should fit snugly into the routed section, requiring precise measurements and cutting. Once in place, the inlay is glued, and after curing, the entire surface is sanded smooth and finished. This technique not only repairs the tearout but also adds a unique, decorative element to the project.
C. Consulting Professionals
For complex or high-value plywood repair projects, seeking assistance from professional woodworkers or furniture refinishers is often the best course of action. Professionals possess the skills, tools, and experience necessary to tackle intricate repairs, ensuring the finished product meets high-quality standards. Whether it involves replicating historical furniture elements or executing precise repairs that are virtually undetectable, professional input can be invaluable. Consulting with a specialist can also provide insight into the best materials and techniques for a particular project, ensuring durability and aesthetic coherence.
Each advanced repair technique offers a distinct approach to restoring and enhancing plywood projects. Whether opting for a DIY solution like veneer patching or router inlay or turning to a professional for expert assistance, the key is to execute the repair with precision and care, ensuring the longevity and beauty of the plywood piece.
Frequently Asked Questions
Q1. How Often Should I Sharpen My Woodworking Tools?
Sharpening frequency depends on use, but as a general rule, tools should be sharpened as soon as you notice a decline in performance. Regular inspections can help identify when sharpening is needed.
Q2. Can I Repair Tearout on Painted Plywood Surfaces?
Yes, tearout on painted surfaces can be repaired. First, fill the damaged area with wood filler, sand it smooth once dry, and then repaint the surface for a seamless finish.
Q3. What Type of Adhesive Is Best for Veneer Patching?
Adhesives like cold press veneer glue or woodworkers’ PVA glue are suitable for veneer patching due to their strong bonding properties and longer open time, which allows for adjustments before setting.
Q4. How Can I Prevent Plywood from Splintering when Cutting?
To prevent splintering, ensure you’re using a sharp blade and consider placing a piece of painter’s tape along the cut line. Also, using a zero-clearance insert on your saw can greatly reduce splintering.
Q5. Is It Necessary to Consult Professionals for All Plywood Repair Projects?
Consulting professionals aren’t required for all projects, especially if you’re comfortable with DIY methods. However, professional expertise can be valuable for complex repairs or when high-quality results are crucial.
Q6. Can Router Inlays Be Used on Curved Surfaces?
Router inlays can be applied to curved surfaces, but the process requires more precision and careful preparation. Using a template and a router with a guide bushing will help achieve more accurate results.
Q7. How Do I Choose the Right Speed for Cutting Different Types of Plywood?
The right speed varies depending on the plywood’s density and thickness. Start with a slower speed for denser materials and adjust according to how the material responds to cutting, aiming for a balance between speed and cut quality.
Conclusion
In this guide, we have explored how to fix plywood tearout by adhering to essential steps and employing both basic and advanced repair techniques. From using sharp blades and adjusting cutting speed to supporting wood grain, these methods emphasize the importance of proper assessment and preparation. Equally, we’ve dived into sophisticated techniques like veneer patching, router inlays, and the value of consulting professionals for complex repairs.
By understanding and implementing these strategies, woodworkers can significantly mitigate the risks associated with plywood tearout, ensuring a successful repair. This underscores the criticality of choosing the right tools, techniques, and care to achieve a resilient and visually pleasing plywood surface.
Ultimately, the satisfaction gained from restoring plywood with precision and diligence highlights the rewarding nature of woodworking. Through careful assessment, preparation, and the application of appropriate repair methodologies, we ensure our plywood projects attain both beauty and longevity.
About the Author
Adrian Green, a lifelong woodworking enthusiast, shares his passion for the craft through The Woodenify Blog. With a foundation built on years of hands-on experience in his father’s woodworking shop, Adrian is dedicated to helping others learn and grow in the world of DIY woodworking. His approach to woodworking combines creativity, practicality, and a deep appreciation for the art of building with your own hands. Through his blog, he inspires individuals of all skill levels to embark on their own woodworking journeys, creating beautiful, functional pieces of furniture and décor.
Professional Focus
- Specializes in DIY woodworking projects, from furniture to home décor.
- Provides step-by-step guides and practical tutorials for woodworkers of all skill levels.
- Dedicated to helping readers build confidence and skill through easy-to-follow instructions and tips.
- Passionate about fostering a community of makers who can share, learn, and grow together.
Education History
- University of Craft and Design – Bachelor of Fine Arts (BFA) in Woodworking and Furniture Design
- Woodworking Apprenticeships – Extensive hands-on training with skilled craftsmen to refine carpentry and furniture making techniques.
- Online Courses & Masterclasses – Continued education in advanced woodworking techniques, design principles, and specialized tools
Expertise:
- DIY woodworking, carpentry, furniture making, and home décor projects.
- Creating accessible tutorials and guides for beginner to advanced woodworkers.
- Sharing the joys and satisfaction of woodworking, from raw materials to finished products.