Medium Density Fiberboard (MDF) is an engineered wood product widely utilized in furniture manufacturing, cabinetry, and interior design due to its affordability, versatility, and uniformity. Composed of wood fibers glued together under heat and pressure, MDF offers a smooth, defect-free surface that is ideal for painting and veneering. Unlike natural wood, MDF does not have knots or grain patterns, which allows for more precise cutting and shaping. This stability makes it a popular choice for intricate designs and detailed craftsmanship.
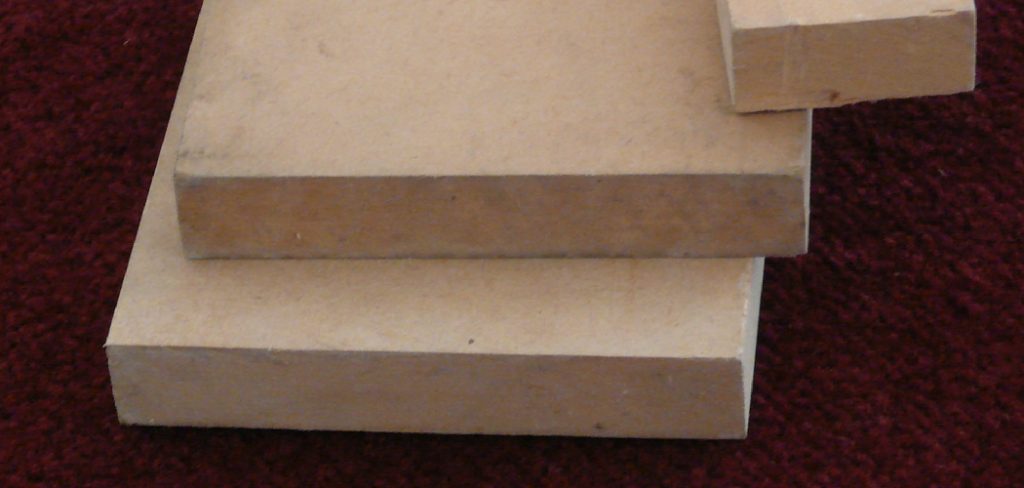
Additionally, MDF is environmentally friendly, often made from recycled wood fibers and byproducts. However, it has some drawbacks, such as its susceptibility to moisture and the need for proper sealing to prevent swelling. Despite these limitations, MDF’s cost-effectiveness and ease of workability have made it a staple in modern woodworking and home improvement projects. This article will explore the properties, benefits, and applications of what is MDF wood, providing a comprehensive understanding of this essential material.
Importance of Understanding MDF
Grasping the intricacies of Medium Density Fiberboard (MDF) is essential for both amateur and professional woodworkers. Knowledge of MDF’s properties can significantly impact the quality and durability of the projects undertaken. For instance, understanding its susceptibility to moisture can guide decisions regarding its use in various environments, especially in areas prone to humidity.
Moreover, awareness of its smooth surface and lack of natural defects allows for better planning in terms of finishing techniques, such as painting or veneering. Being informed about the need for proper sealing can prevent potential issues like swelling and warping, thereby extending the lifespan of the finished product. Ultimately, a comprehensive understanding of MDF enables more informed choices, resulting in high-quality, cost-effective, and long-lasting woodworking projects.
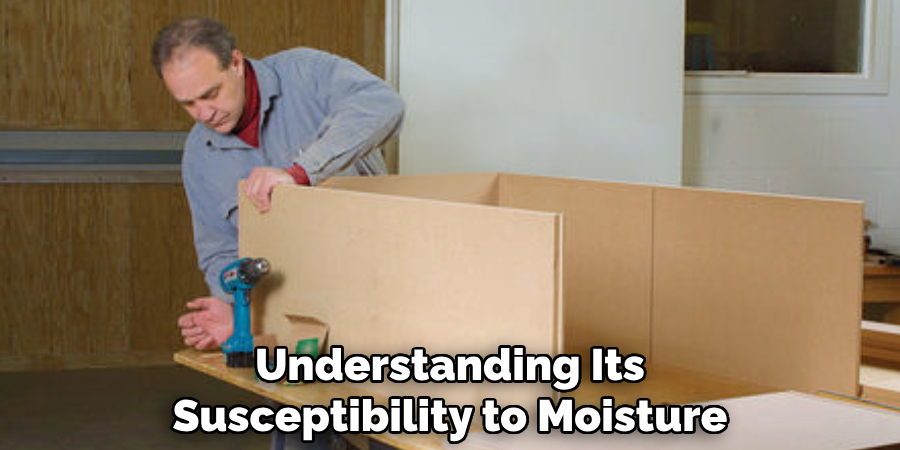
Definition of MDF
Medium Density Fiberboard (MDF) is an engineered wood product that is manufactured by breaking down hardwood or softwood residuals into wood fibers, often in a defibrator, combining it with wax and a resin binder, and forming panels by applying high temperature and pressure.
The result is a dense, uniform board that boasts a smooth surface and consistent texture, making it ideal for precise machining and perfect for a variety of detailed woodworking applications. MDF typically has a higher density than plywood and is free from the knots and grain patterns found in natural wood, making it an excellent choice for custom millwork, furniture, and cabinetry. Its homogeneous structure enables reliable finishing and an appearance that can easily be tailored to specific design requirements through painting, laminating, or veneering.
How MDF is Manufactured
The manufacturing process of Medium Density Fiberboard (MDF) involves several distinct stages designed to turn wood residuals into a durable and uniform engineered wood product. The initial step entails the collection and sorting of hardwood and softwood residuals, which are then subjected to a process called defibration. In this process, the wood chips are broken down into fine wood fibers using steam and mechanical forces.
Following defibration, the wood fibers are mixed with wax and a resin binder to enhance the board’s strength and stability. This mixture is then formed into a mat, which is subsequently compressed under high pressure and temperature to create a dense, uniform panel. During compression, the high temperature activates the resin binder, allowing the fibers to bond together firmly.
After the board takes shape, it is cooled and trimmed to the desired size. The final product is then sanded to ensure a smooth surface, making it ready for further finishing processes such as painting, laminating, or veneering. Throughout the manufacturing process, quality control measures are implemented to ensure the MDF meets stringent standards for density, thickness, and uniformity. This meticulous manufacturing process results in a versatile and reliable material widely used in numerous woodworking and interior design applications.
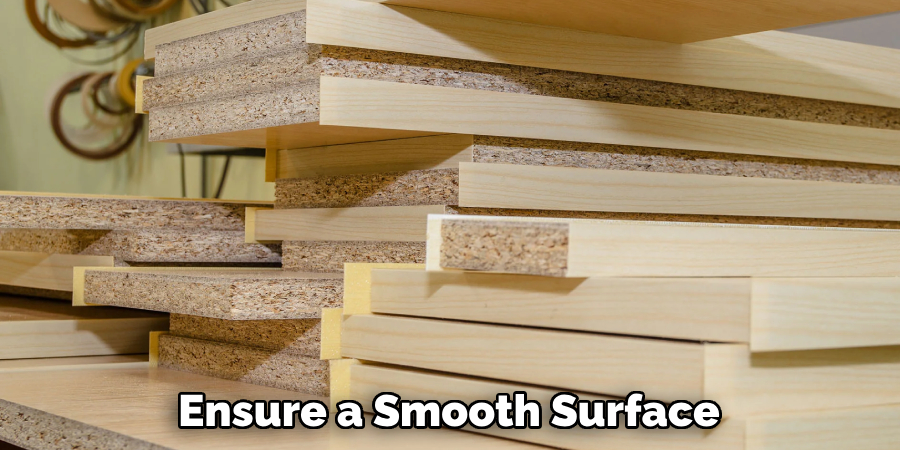
9 Ways to Understand What Is Mdf Wood
1. Composition and Manufacturing Process
MDF is made from wood fibers, which are the residue left after wood is processed. These fibers are combined with resin binders and wax, then subjected to high temperature and pressure to form dense, flat panels. The manufacturing process involves breaking down softwood or hardwood into fibers, which are then dried and mixed with adhesive.
The mixture is formed into panels and compressed under heat, creating a uniform and dense board with smooth surfaces on both sides. This process ensures that MDF is free from the natural imperfections found in solid wood, such as knots and grain variations.
2. Physical Properties
MDF’s uniform density and smooth surface make it an excellent material for various woodworking applications. It typically has a density of 600-800 kg/m³, which provides a good balance between strength and weight.
The lack of grain structure means MDF can be cut, drilled, and machined without chipping or splintering, making it ideal for detailed and intricate designs. Additionally, MDF has excellent dimensional stability, meaning it won’t warp or expand significantly with changes in humidity and temperature, unlike solid wood.
3. Advantages of Using MDF
One of the main advantages of MDF is its affordability compared to solid wood and other engineered wood products like plywood. Its consistent composition allows for precise machining and finishing, which is particularly beneficial for applications requiring intricate cuts and shapes.
MDF is also available in larger sizes than most solid wood boards, reducing the need for seams and joints in large projects. Its smooth surface is perfect for painting, veneering, and laminating, providing a high-quality finish. Additionally, MDF is often made from recycled wood fibers, making it an environmentally friendly option.
4. Common Uses in Furniture Making
MDF is extensively used in furniture manufacturing due to its versatility and cost-effectiveness. It is commonly found in ready-to-assemble furniture, cabinets, shelves, and storage units. Its smooth surface is ideal for applying veneers or laminates, allowing manufacturers to mimic the appearance of solid wood at a lower cost.
MDF is also used for creating detailed moldings, trims, and decorative elements in furniture design, as it can be easily machined into complex shapes without splintering.
5. Applications in Interior Design
In interior design, MDF is a popular choice for wall paneling, wainscoting, baseboards, and crown molding. Its smooth surface and ability to hold paint well make it suitable for creating sleek, modern finishes or traditional, ornate designs.
MDF can be cut into various shapes and patterns, allowing designers to customize and personalize interior spaces. Additionally, its stability and resistance to warping make it an excellent material for door panels and window sills.
6. Workability and Machining
MDF’s consistent density and lack of grain make it highly workable with standard woodworking tools. It can be cut, drilled, routed, and shaped with ease, providing a clean edge and smooth surface.
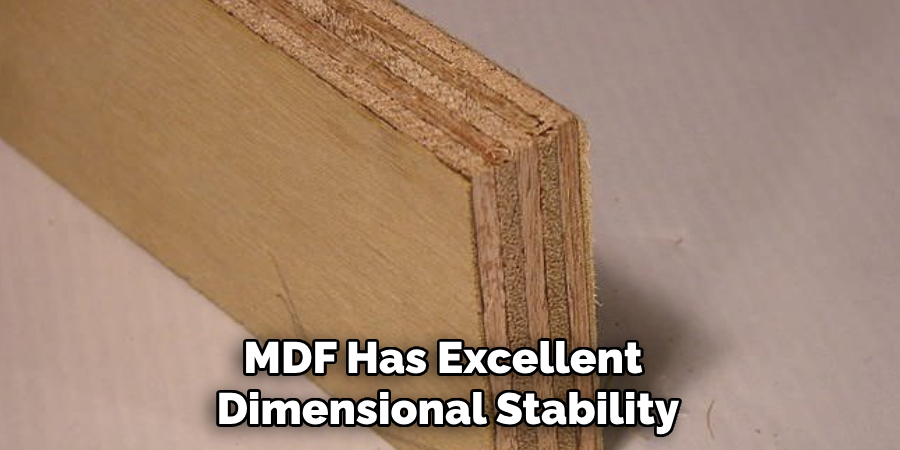
This workability is particularly advantageous for creating detailed and precise designs, such as decorative moldings and intricate joinery. However, MDF produces a fine dust when machined, so proper dust extraction and personal protective equipment, such as masks and goggles, are essential to ensure a safe working environment.
7. Finishing Techniques
One of MDF’s standout features is its ability to accept a variety of finishes. Its smooth surface is ideal for painting, allowing for a flawless, high-quality finish with minimal preparation. MDF can also be veneered with thin slices of real wood, providing the appearance of solid wood at a fraction of the cost.
Lamination is another popular finishing technique, where decorative laminates are glued to the MDF surface to create a durable and attractive finish. Additionally, MDF can be covered with adhesive-backed films or foils for a quick and easy decorative solution.
8. Environmental Impact
MDF is often considered an environmentally friendly option because it utilizes wood fibers and byproducts that would otherwise be wasted. Many MDF manufacturers use recycled wood materials, contributing to sustainable forest management practices.
Additionally, MDF production requires less energy and resources compared to the processing of solid wood and other engineered wood products. However, it’s important to note that MDF contains formaldehyde-based resins, which can off-gas volatile organic compounds (VOCs). To mitigate this, look for MDF products that are certified as low-emission or made with alternative, low-formaldehyde adhesives.
9. Potential Drawbacks and Considerations
While MDF has many advantages, there are also some potential drawbacks to consider. Its susceptibility to moisture is a significant concern, as MDF can swell and deteriorate when exposed to water.
Therefore, it is not recommended for outdoor use or in areas with high humidity, such as bathrooms and kitchens, unless properly sealed. MDF’s weight can also be an issue, as it is denser and heavier than many types of solid wood, making it more challenging to handle and transport. Additionally, the fine dust produced during machining can pose health risks, so proper ventilation and protective equipment are essential.
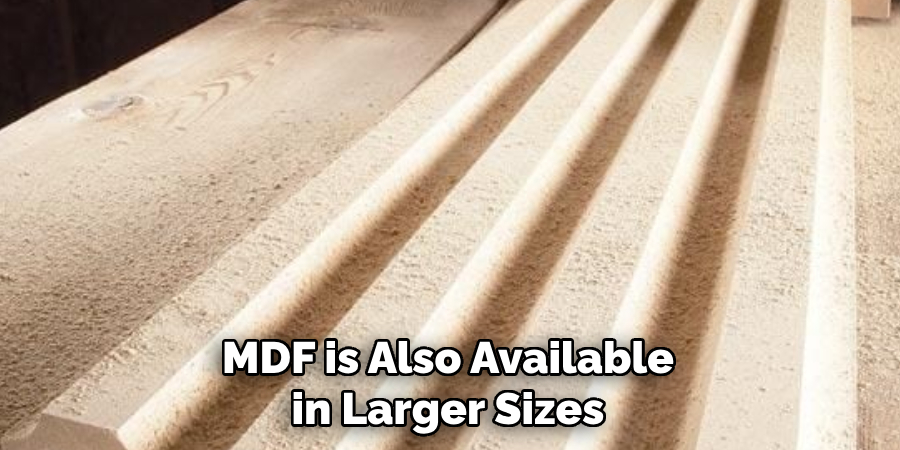
Conclusion
Medium Density Fiberboard (MDF) is a versatile and cost-effective material that offers numerous benefits for woodworking and interior design projects. Its uniform composition, smooth surface, and ease of machining make it an excellent choice for furniture making, cabinetry, and decorative elements.
While it has some potential drawbacks, such as moisture susceptibility and formaldehyde emissions, proper handling and finishing techniques can mitigate these issues. Thanks for reading, and we hope this has given you some inspiration on what is mdf wood!
About the Author
Adrian Green, a lifelong woodworking enthusiast, shares his passion for the craft through The Woodenify Blog. With a foundation built on years of hands-on experience in his father’s woodworking shop, Adrian is dedicated to helping others learn and grow in the world of DIY woodworking. His approach to woodworking combines creativity, practicality, and a deep appreciation for the art of building with your own hands. Through his blog, he inspires individuals of all skill levels to embark on their own woodworking journeys, creating beautiful, functional pieces of furniture and décor.
Professional Focus
- Specializes in DIY woodworking projects, from furniture to home décor.
- Provides step-by-step guides and practical tutorials for woodworkers of all skill levels.
- Dedicated to helping readers build confidence and skill through easy-to-follow instructions and tips.
- Passionate about fostering a community of makers who can share, learn, and grow together.
Education History
- University of Craft and Design – Bachelor of Fine Arts (BFA) in Woodworking and Furniture Design
- Woodworking Apprenticeships – Extensive hands-on training with skilled craftsmen to refine carpentry and furniture making techniques.
- Online Courses & Masterclasses – Continued education in advanced woodworking techniques, design principles, and specialized tools
Expertise:
- DIY woodworking, carpentry, furniture making, and home décor projects.
- Creating accessible tutorials and guides for beginner to advanced woodworkers.
- Sharing the joys and satisfaction of woodworking, from raw materials to finished products.