Selecting the right band saw blade is crucial for any woodworking project. The correct blade can make a remarkable difference in the quality and efficiency of your cuts, whether you are working with hardwood or softwood, making straight cuts or intricate curves. Understanding how to choose the correct band saw blade wood can significantly enhance your woodworking experience.
Using the appropriate band saw blade for your specific needs leads to improved performance, higher efficiency, and superior quality of cuts. A well-chosen blade reduces the risk of mistakes and material wastage and ensures smoother, cleaner results. It also increases the lifespan of your equipment by reducing wear and tear.
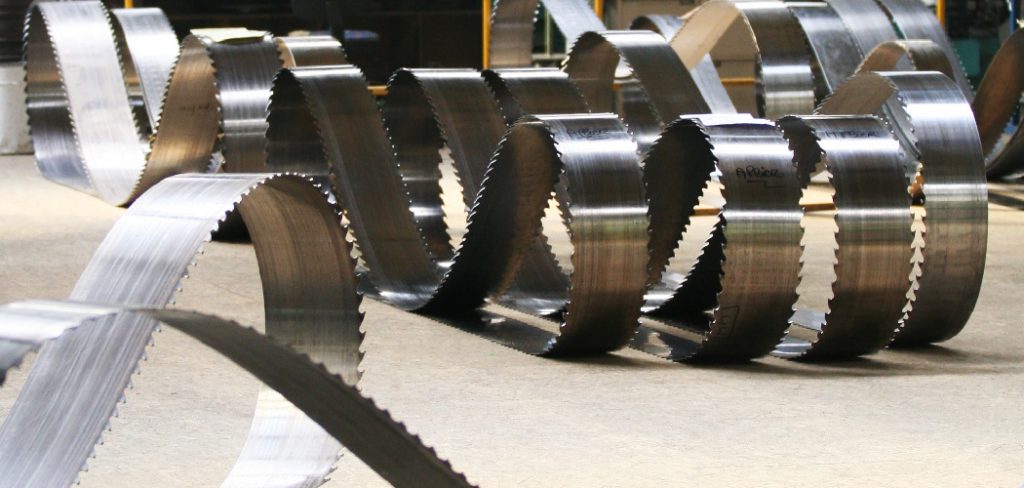
This guide will provide a structured approach to how to choose the correct band saw blade wood. We will cover the basics of blade types, materials, and construction, as well as how to match your blade to various cutting needs and wood types. Additionally, we will delve into blade maintenance and troubleshooting common issues to help you achieve the best possible outcomes in your woodworking projects.
Understanding Band Saw Blade Basics
A. Types of Band Saw Blades
There are several types of band saw blades, each tailored to specific cutting tasks. The Hook Tooth blade is characterized by its large, aggressive teeth and deep gullets, which efficiently remove material and are ideal for fast, rough cuts in thick wood and non-ferrous metals.
Skip Tooth blades feature widely spaced teeth with shallow gullets that help evacuate sawdust, making them suitable for softwoods and plastics. Regular Tooth blades have evenly spaced, smaller teeth and are designed for general-purpose use, providing smooth and precise cuts in various materials, including hardwoods and plastics.
B. Blade Terminology
Understanding specific blade terminology is crucial in selecting the appropriate band saw blade for your project. TPI (Teeth Per Inch) refers to the number of teeth along a one-inch section of the blade; a higher TPI means a finer, slower cut, while a lower TPI indicates a faster, rougher cut.
Tooth Set describes the pattern in which the teeth are angled or bent; common configurations include Straight Set, Raker Set, and Alternate Set, each affecting the cut’s quality and speed. Blade Width measures the distance from the back of the blade to the tip of the tooth, impacting the blade’s ability to cut tight curves and maintain stability.
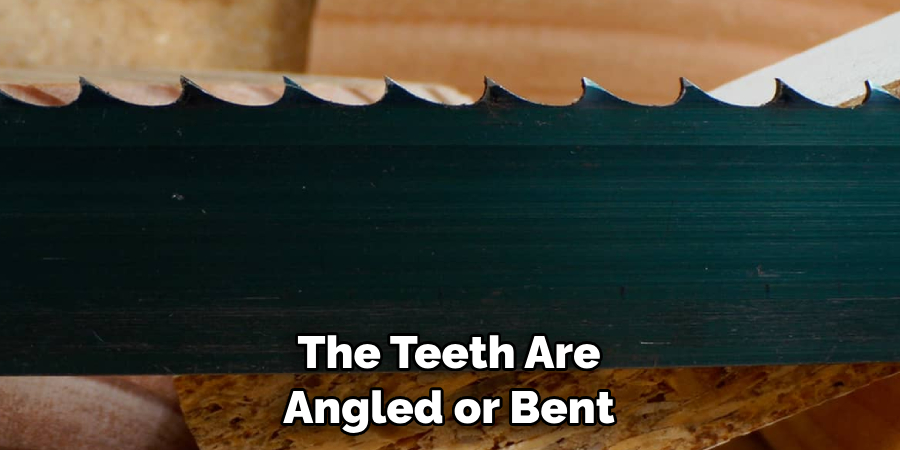
Blade Thickness, the measurement of the blade from one surface to the other, affects its durability and flexibility. Thicker blades are more robust but less flexible, while thinner blades are more flexible but prone to breakage.
C. Materials and Construction
Band saw blades are constructed from various materials, each offering different strengths and applications. Carbon Steel blades are economical and suitable for cutting softwoods and some plastics; however, they wear out quickly on harder materials.
Bi-Metal blades combine a high-speed steel edge with a flexible alloy steel backing, offering durability, versatility, and the ability to cut both wood and metal. Carbide-tipped blades boast teeth made from tungsten carbide, providing exceptional longevity and precision, particularly valuable for cutting dense hardwoods, composites, and abrasive materials. Understanding these materials’ characteristics will help you choose the most suitable blade for your projects.
How to Choose the Correct Band Saw Blade Wood: Identifying Your Cutting Needs
A. Types of Cuts
Understanding the types of cuts you will be making is a crucial step in selecting the right band saw blade. Rip Cuts are made along the grain of wood and require a blade with a low TPI to remove material quickly. Crosscuts, on the other hand, are made across the wood grain and need a blade with a higher TPI to produce smoother finishes.
Resawing refers to cutting a piece of wood along its thickness to create thinner slabs; for this, a wide blade with a few TPI is ideal to maintain stability and remove large amounts of material efficiently. Curve Cuts are intricate cuts that require a thin blade with a high TPI to navigate tight radii without bending or breaking. Each type of cut places different demands on the blade, making it essential to match the blade type to the specific cutting task.
B. Wood Types
The type of wood you are working with significantly influences your blade choice. Hardwoods like oak, maple, and walnut have dense fibers that can quickly dull a standard blade. Using a bi-metal or carbide-tipped blade ensures longevity and clean cuts for these materials.
Softwoods such as pine, fir, and cedar are easier to cut and can be handled effectively with carbon steel blades, which are more economical. When dealing with Composite Materials like plywood or MDF, which can contain glue and other binding agents, a blade with larger, widely spaced teeth will help to reduce gumming and extend blade life. Each wood type’s specific characteristics will dictate the best blade material, TPI, and tooth configuration for optimal performance and efficiency.
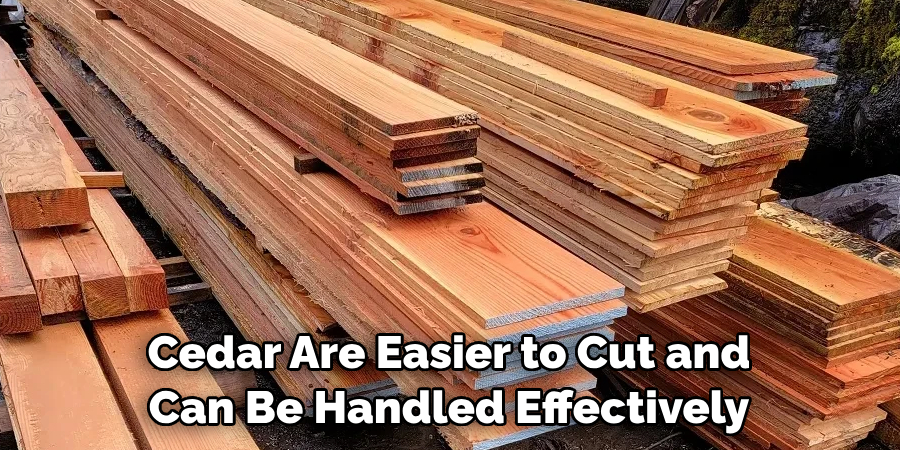
C. Desired Finish
The final consideration when choosing a band saw blade is your cut’s desired smoothness and finish. If you aim for a coarse, rough cut, perhaps for the initial stages of material removal, a blade with a low TPI will provide a faster, rougher finish. Conversely, if you need fine, smooth cuts, especially for final finish work, a blade with a high TPI is essential to achieve the level of detail and smoothness required.
Additionally, the tooth set and blade material can impact the quality of the finish; for example, a carbide-tipped blade with an alternate tooth set is perfect for delicate, near-polished cuts in hard or composite materials. By considering the desired finish, you can choose a blade that not only meets your cutting specifications but also delivers the quality of craftsmanship you seek in your woodworking projects.
How to Choose the Correct Band Saw Blade Wood: Blade Width and Thickness
A. Blade Width: Choosing the Appropriate Width for Different Types of Cuts and Curves
Blade width determines the range of cutting tasks your band saw can handle. Wider blades, typically used for straight cuts like resawing, offer enhanced stability, making them ideal for aggressive material removal and thin slab creation. For example, a wide blade (3/4 inch to 1 inch) is perfect for resawing thick hardwood slabs, providing the necessary support to maintain a straight cut without wandering.
Conversely, narrow blades, ranging from 1/8 inch to 1/4 inch, are better suited for intricate curve cuts. Their flexibility allows them to navigate tight radii without binding or breaking. Woodworkers aiming to produce detailed patterns or shapes often opt for narrow blades to achieve precision and prevent damage to both the blade and the workpiece. By selecting the appropriate blade width for your cutting needs, you can ensure optimal performance and accuracy for each task.
B. Blade Thickness: Understanding How Thickness Affects Stability and Flexibility
Blade thickness is another crucial factor that influences the performance and durability of your band saw blade. Thicker blades, generally around 0.032 inches to 0.042 inches, offer increased rigidity, making them suitable for heavy-duty cutting and dense materials. This added robustness reduces the likelihood of blade deflection, ensuring cleaner and more accurate cuts in tough woods like oak and maple.
However, the trade-off is decreased flexibility, which can limit the blade’s effectiveness in executing tight curves. On the other hand, thinner blades, with a thickness of about 0.014 inches to 0.025 inches, provide greater flexibility. This makes them excellent for intricate work and detailed patterns but comes at the cost of reduced durability and a higher potential for breakage, particularly when subjected to heavy loads. Balancing thickness based on your cutting requirements will enable you to select a blade that combines the necessary strength and flexibility for each project.
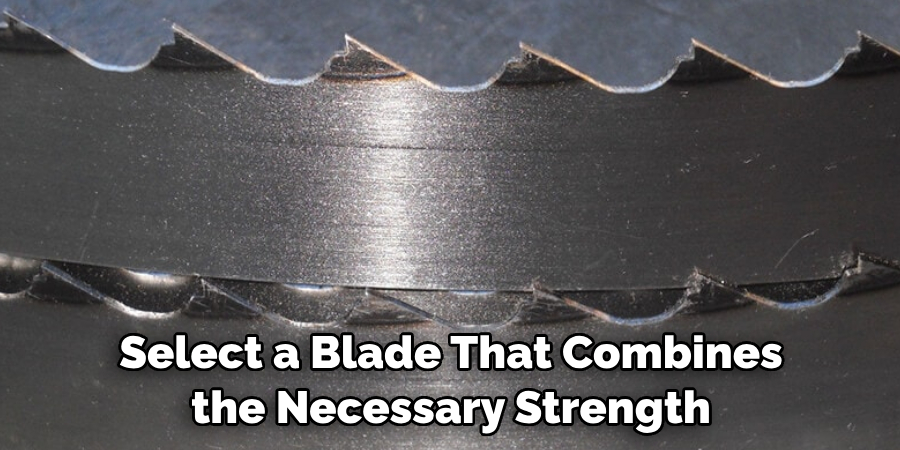
C. Matching Blade Size to Saw Capacity: Ensuring Compatibility with Your Band Saw’s Specifications
To maximize the efficiency and safety of your woodworking projects, it is imperative to match the blade size to your band saw’s capacity. Each band saw is designed to handle specific blade widths and thicknesses, as outlined in the manufacturer’s specifications. Fitting a blade that exceeds your saw’s capacity can result in poor performance, increased wear, and potential damage to your equipment.
For instance, attempting to mount a 1-inch wide blade on a saw designed for a maximum of 3/4-inch width can strain the saw’s components, leading to misalignment and potential safety hazards. Additionally, ensuring the tensioning system can accommodate the blade’s thickness is crucial.
Over-tensioning a thin blade can cause it to snap while under-tensioning a thick blade can result in blade deflection and imprecise cuts. Always refer to your band saw’s manual to confirm the appropriate blade size and adjust the tensioning mechanism accordingly. By ensuring compatibility, you enhance the longevity of your equipment and achieve superior cutting results.
Tooth Configuration
A. TPI (Teeth Per Inch): Selecting the Right TPI for Different Types of Cuts and Materials
TPI, or Teeth Per Inch, is a critical determinant of a saw blade’s cutting ability and the finish of the cut. Blades with a low TPI, ranging from 2 to 6 TPI, have fewer spaced-out teeth, making them ideal for rapid, aggressive cuts in thicker materials. They allow faster material removal and are suitable for coarse cuts in wood and metals.
Conversely, blades with a high TPI, from 14 to 32 TPI, have more teeth per inch and provide smoother finishes, making them perfect for cutting thin materials and achieving detailed, fine cuts. For general-purpose woodworking, a mid-range TPI, such as 8 to 12, is often preferred, balancing speed and smoothness. Selecting the appropriate TPI depends on the material’s thickness and the desired cut quality, ensuring efficiency and precision in every task.
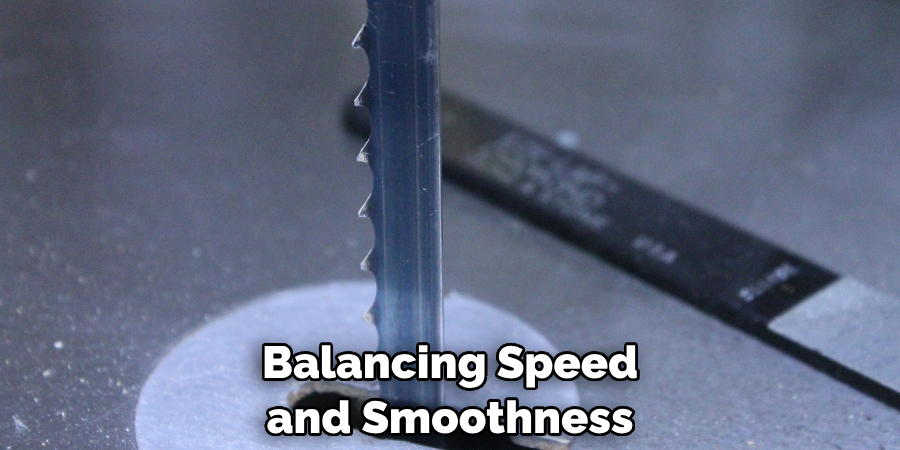
B. Tooth Set: Explaining Straight Set, Raker Set, and Alternate Set and Their Applications
The tooth set refers to the arrangement of the teeth on the blade, which affects the cut’s width and chip removal efficiency.
- Straight Set: The teeth are aligned straight across the blade in this configuration. It is often used for cutting fine, soft materials like thin plastics or softwoods, where minimal material chipping is desired. The straight set ensures a narrow kerf and clean, straight cuts.
- Raker Set: This set features a repetitive pattern of one tooth set to the left, one to the right, and one straight. This arrangement balances chip removal and cut efficiency, making it versatile for various materials, including hardwoods, metals, and plastics. The raker set is ideal for both straight and contour cuts, providing a smooth finish and efficient debris ejection.
- Alternate Set: Teeth are alternately set left and right, providing excellent chip clearance and reducing the risk of blade binding. This set is well-suited for aggressive cuts in dense and composite materials, such as hardwoods, particleboard, and plywood. It offers fast, rough cuts with less chance of overheating and decreased blade life.
Each tooth set has its specific application, and choosing the right one maximizes performance and material management during cutting operations.
C. Tooth Shape: Comparing Hook Tooth, Skip Tooth, and Regular Tooth Blades for Various Tasks
Tooth shape influences a blade’s performance, handling different materials and cut types.
- Hook Tooth: These teeth have a positive rake angle, allowing for aggressive, deep cuts. Hook tooth blades are especially effective in cutting thick or hard materials, such as hardwoods or metals, as their design facilitates rapid chip removal and reduces cutting resistance. They are ideal for situations requiring fast cutting and high material removal rates.
- Skip Tooth: Featuring a wide gap between teeth, skip tooth blades excel in cutting soft woods, plastics, and non-ferrous metals. The large gullet between teeth prevents clogging, ensuring efficient chip clearance and reducing overheating risks. This tooth shape is perfect for ripping and resawing, providing clean, fast cuts.
- Regular Tooth: With evenly spaced teeth and a straight rake angle, regular tooth blades deliver smooth, precise cuts in thinner materials. They are commonly used for detailed work and fine finishes in both woodworking and metalworking, offering balance and control for intricate tasks.
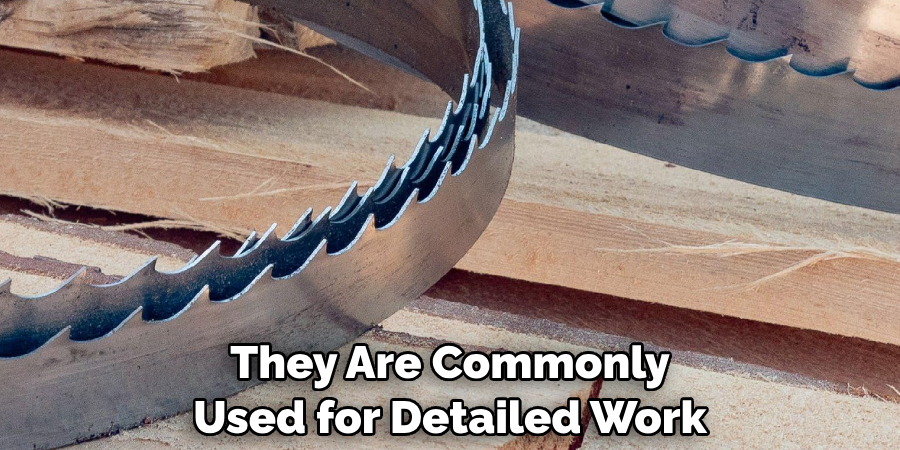
Understanding the nuances of tooth shape allows for informed blade selection, ensuring optimal performance and cut quality for each specific material and task. Woodworkers can enhance their cutting efficiency, achieve superior finishes, and extend blade longevity by carefully considering TPI, tooth set, and tooth shape.
Specialty Blades
A. Resawing Blades: Choosing Blades Designed for Resawing and Thick Material Cuts
Resawing blades specialize in slicing through thick boards or logs to create thinner slabs, veneers, or book-matched pieces. These blades typically have fewer teeth per inch (TPI), often in the 1 to 3 TPI range, promoting efficient chip removal and reducing the risk of wood burning. The wider blade width, generally around 3/4 inch to 1 inch, ensures stability and straight cuts, which is critical for maintaining even surfaces over long cutting distances.
When selecting a resawing blade, consider the material’s hardness and the blade’s gullet size to prevent clogging and maintain smooth operations. Resawing thick materials requires a sturdy, properly tensioned blade capable of withstanding the demands of high-pressure cutting, ensuring both precision and safety during use.
B. Scroll Blades: Selecting Blades for Intricate and Detailed Curve Cuts
Scroll blades are designed for cutting tight curves, intricate patterns, and detailed shapes in thin materials such as wood, plastic, and metal. Typically, these blades have a high TPI range, from 10 to 15 TPI, allowing for fine, precise cuts without splintering or tearing the material. Their narrow blade width, often between 1/8 inch to 1/4 inch, provides the flexibility needed to navigate sharp turns and complex designs.
Selecting the right scroll blade involves considering the material’s thickness and the level of detail required for the project. Fine scroll blades excel in detailed work, while coarser options are better for faster, less intricate cuts. Always ensure the blade is sharp and tensioned correctly to maintain control and achieve the desired results in scrollwork.
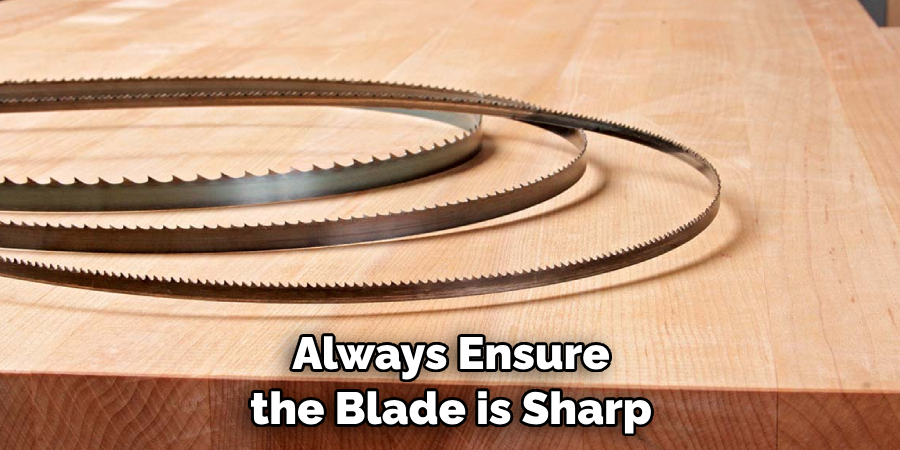
C. Carbide-Tipped Blades: Benefits and Uses of Carbide-Tipped Blades for Longevity and Precision
Carbide-tipped blades combine robust steel bodies with carbide tooth tips, enhancing durability and cutting performance. These blades are renowned for their longevity, maintaining sharpness significantly longer than standard steel blades, even when cutting hard materials like hardwoods, composites, and metals.
The carbide tips provide excellent wear resistance, reducing the frequency of blade changes and ensuring consistent precision over extended periods. Carbide-tipped blades are ideal for tasks requiring high accuracy and smooth finishes, such as fine woodworking, cabinetry, and metalworking. They excel in applications where superior cut quality and extended blade life are paramount, making them a valuable investment for woodworkers seeking efficiency and reliability in their cutting tools.
Matching the Blade to the Task
A. General Purpose Blades: When to Use General Purpose Blades for Versatility
General-purpose blades are designed to handle various cutting tasks, making them a staple in any woodworker’s toolkit. These blades typically feature a moderate tooth count, often around 40 to 50 teeth, which allows them to perform both rip cuts and crosscuts effectively. The tooth geometry is usually optimized to balance cutting speed and finish quality. General-purpose blades are ideal for tasks requiring versatility, such as building furniture, cabinetry, or constructing DIY projects.
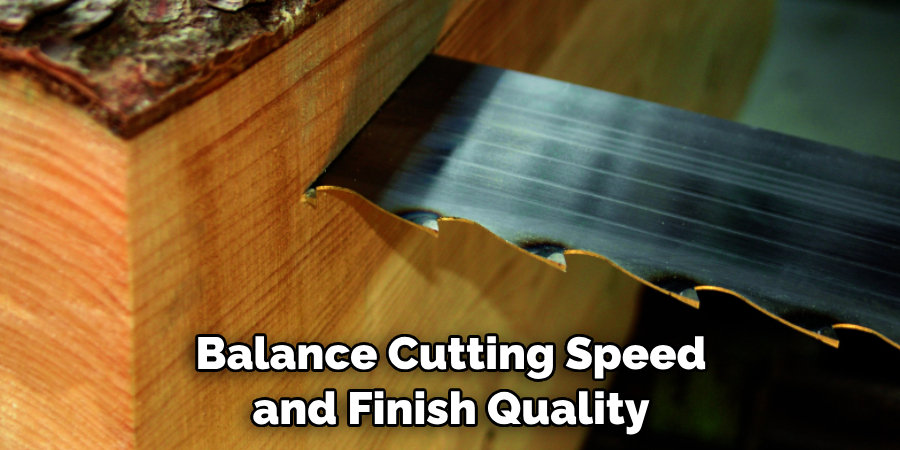
They are particularly useful when switching between different types of wood or composite materials, as their design can handle the varied density and grain structures without the need for frequent blade changes. Employing a general-purpose blade for everyday tasks can save time and improve workflow efficiency, making it a valuable addition to any workshop.
B. Fine Finish Blades: Choosing Blades for Smooth, Fine Finishes in Detailed Work
Fine finish blades are specialized for producing exceptionally smooth cuts, crucial for detailed work and projects requiring a high-quality finish. These blades often have a high tooth count, generally ranging from 60 to 100 teeth, enabling them to cut with precision and minimal tear-out. The teeth are typically smaller and have a higher bevel angle, which ensures clean edges and a polished surface.
Fine finish blades are ideal for tasks such as trim work, cutting veneers, or creating intricate joinery, where the quality of the cut surface is of utmost importance. When choosing a fine finish blade, consider the type of material, the desired finish, and the blade’s compatibility with your saw. Using a fine finish blade can significantly reduce the need for additional sanding or finishingrigors enhancing the overall quality of your work.
C. Heavy-Duty Blades: Selecting Blades for Heavy-Duty Tasks and Thick Wood Cutting
Heavy-duty blades are engineered to withstand the rigors of cutting thick and hard materials, making them indispensable for demanding woodworking tasks. These blades often feature fewer teeth, usually in the range of 24 to 30, which provides greater space between the teeth for effective chip removal and reduced heat buildup.
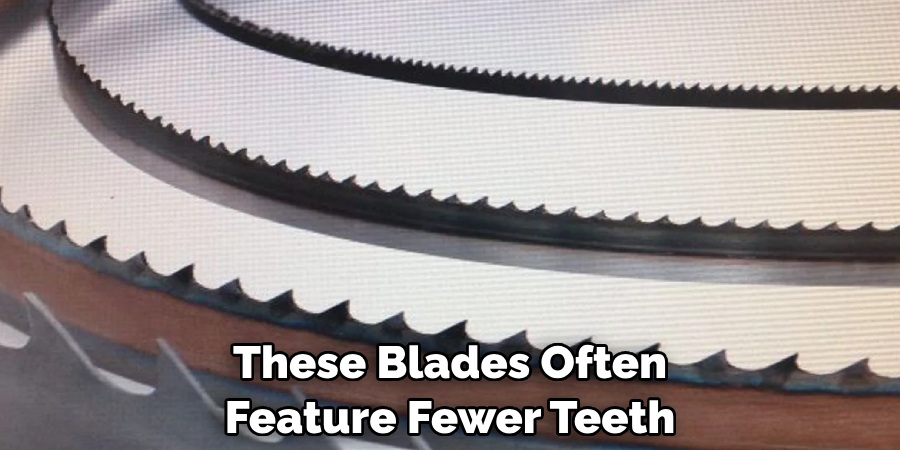
The larger, more robust teeth and thicker blade body ensure durability and stability when cutting through dense hardwoods, pressure-treated lumber, or reclaimed wood. Heavy-duty blades are perfect for tasks such as framing, timber construction, or cutting large beams and logs. When selecting a heavy-duty blade, consider the material’s hardness, moisture content, and the specific requirements of your project.
Using a blade designed for heavy-duty applications ensures effective cutting and enhances your tools’ safety and longevity. By matching the right blade to the task, woodworkers can achieve optimal performance, maintain cutting precision, and extend the life of their blades.
Blade Maintenance and Care
A. Cleaning the Blade: Importance of Regular Cleaning to Maintain Performance
Regular cleaning of your blades is crucial to maintain their cutting performance and extend their lifespan. Over time, blades accumulate resin, pitch, sap, and other debris, hindering their effectiveness.
A dirty blade cuts less efficiently, requires more force, and can overheat, leading to quicker dulling and potential damage. Remove a blade from the saw and use a brush or cloth with a specialized blade cleaner or a mixture of water and mild detergent. Gently scrub away the buildup, paying attention to the teeth and gullets. Rinse thoroughly and dry the blade before reinstalling it. Regular cleaning ensures smooth, precise cuts and reduces wear and tear on your saw, contributing to overall better performance and safety.
B. Sharpening and Replacing: Knowing When to Sharpen or Replace Blades
Sharpening your blades at the right time is key to maintaining their cutting efficiency and prolonging their usability. Signs that a blade needs sharpening include difficulty cutting, increased burning or tearing of the material, and an uneven or rough finish. Regular maintenance sharpening can keep blades in top condition depending on usage and the type of blade.
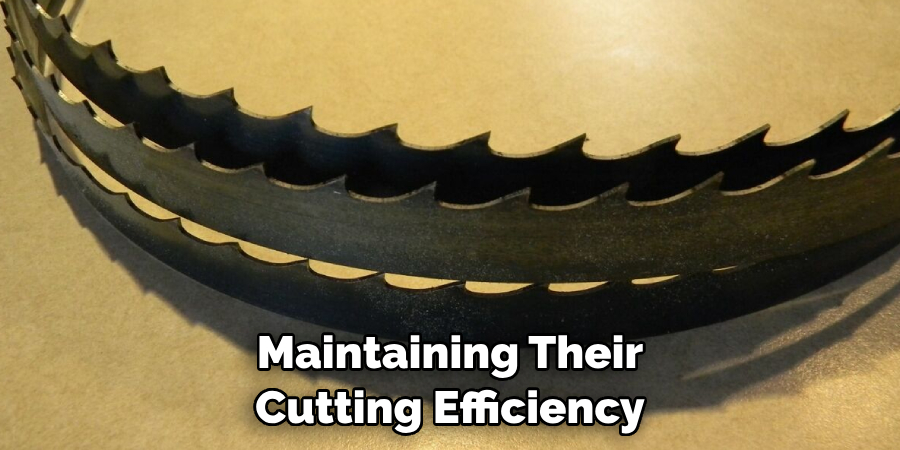
However, carbide-tipped blades require professional sharpening due to the hardness of the material. Once a blade has been sharpened multiple times and its diameter has significantly reduced, or if teeth are missing or broken, it is time to replace it. Investing in high-quality blades and maintaining them properly can save costs in the long term by reducing the frequency of replacements.
C. Proper Storage: Tips for Storing Blades to Prevent Damage and Prolong Life
Proper storage of blades is essential to prevent damage and ensure their longevity. Store blades in a dry, cool place to avoid rust and corrosion. Use blade storage racks or cases to keep them organized and to prevent them from knocking against each other, which can dull or chip the teeth. If storing blades on hooks or nails, ensure they hang individually and do not touch.
For additional protection, consider placing a piece of cardboard or wood between the blades to avoid contact. Label each blade’s type and tooth count to easily identify them for different tasks. By implementing these storage practices, you can maintain blade sharpness and functionality, ensuring they are ready for use whenever needed.
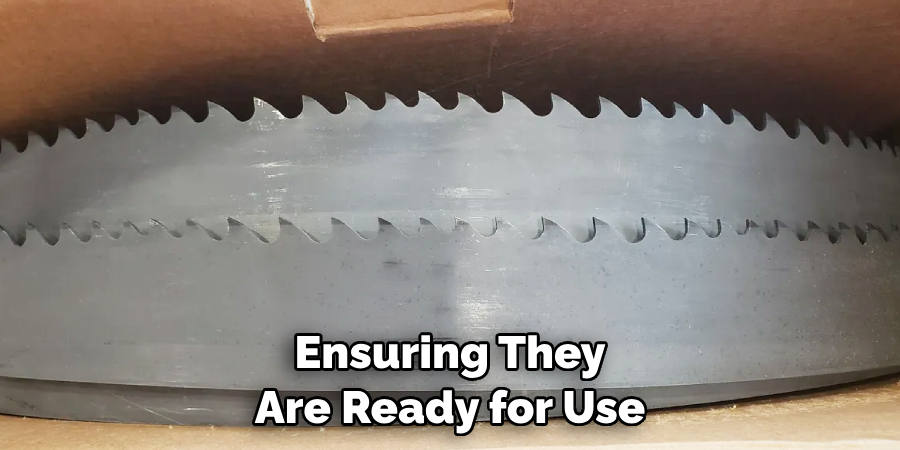
Conclusion
Proper blade care and selection are fundamental to achieving precise and efficient cuts in woodworking and other cutting tasks. From regular cleaning to timely sharpening and meticulous storage, each step plays a vital role in maintaining the blade’s performance and longevity. Troubleshooting common issues such as blade drift and breakage can mitigate problems before they disrupt your work.
Moreover, seeking expert advice, testing various blades, and keeping thorough records helps tailor your approach to your specific needs and enhances overall proficiency. Implementing these strategies ensures that your blades deliver consistent, high-quality results, contributing to safer and more effective woodworking projects. Thanks for reading our blog post about how to choose the correct band saw blade wood cutting, we hope you found it informative and helpful! Happy woodworking!
About the Author
Adrian Green, a lifelong woodworking enthusiast, shares his passion for the craft through The Woodenify Blog. With a foundation built on years of hands-on experience in his father’s woodworking shop, Adrian is dedicated to helping others learn and grow in the world of DIY woodworking. His approach to woodworking combines creativity, practicality, and a deep appreciation for the art of building with your own hands. Through his blog, he inspires individuals of all skill levels to embark on their own woodworking journeys, creating beautiful, functional pieces of furniture and décor.
Professional Focus
- Specializes in DIY woodworking projects, from furniture to home décor.
- Provides step-by-step guides and practical tutorials for woodworkers of all skill levels.
- Dedicated to helping readers build confidence and skill through easy-to-follow instructions and tips.
- Passionate about fostering a community of makers who can share, learn, and grow together.
Education History
- University of Craft and Design – Bachelor of Fine Arts (BFA) in Woodworking and Furniture Design
- Woodworking Apprenticeships – Extensive hands-on training with skilled craftsmen to refine carpentry and furniture making techniques.
- Online Courses & Masterclasses – Continued education in advanced woodworking techniques, design principles, and specialized tools
Expertise:
- DIY woodworking, carpentry, furniture making, and home décor projects.
- Creating accessible tutorials and guides for beginner to advanced woodworkers.
- Sharing the joys and satisfaction of woodworking, from raw materials to finished products.