Creating a resin table mold is a vital step in making a beautiful and unique resin table. A mold acts as a container that shapes the resin as it cures, allowing you to achieve the desired form and style. Essential tools and materials needed for this project include mold materials such as silicone, wood, or melamine, as well as cutting tools, sealants, and release agents.
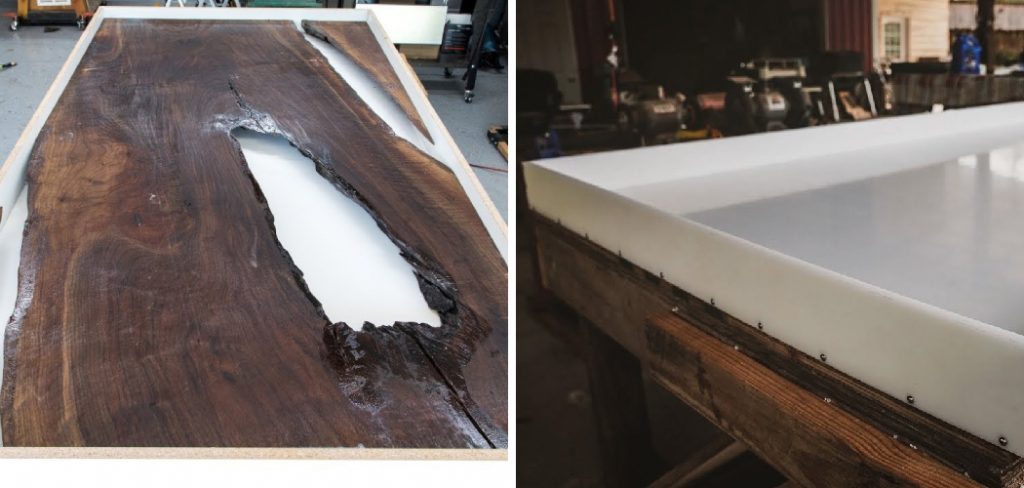
This comprehensive guide will walk you through the steps of how to make a resin table mold, from planning and designing the mold to the final touches. By following our detailed instructions, you will learn how to choose the right materials, cut and shape the mold, and properly prepare it for a successful resin pour.
For DIY enthusiasts, making a custom resin table mold offers a fantastic opportunity for creativity and personalization. Instead of relying on pre-made molds, crafting your mold allows you to design and create table pieces that perfectly match your vision and style, resulting in truly unique furniture pieces.
Planning and Design
Selecting a Design
When selecting a design for your resin table, you’ll need to consider several factors that will influence the final outcome. The shape of the table is one of the primary considerations – whether you prefer a circular, rectangular, or irregular shape will impact the overall aesthetic and functionality.
Size is another critical factor; a larger table requires more material and workspace, while a smaller table may be more manageable for beginners.
Additionally, the style of your resin table can vary from contemporary sleek surfaces to rustic designs incorporating natural wood elements or artistic inclusions like dried flowers and metallic flakes. Visualizing the end product and how it will complement your existing décor will help guide your design choices.
Material Choices
Selecting the right material for your resin table mold is crucial in achieving a professional finish. Silicone is a popular choice due to its flexibility and non-stick properties, making demolding easier. However, it can be relatively expensive.
Wood, such as plywood or MDF, provides a sturdy and cost-effective option, but it requires sealing to prevent the resin from sticking or leaking.
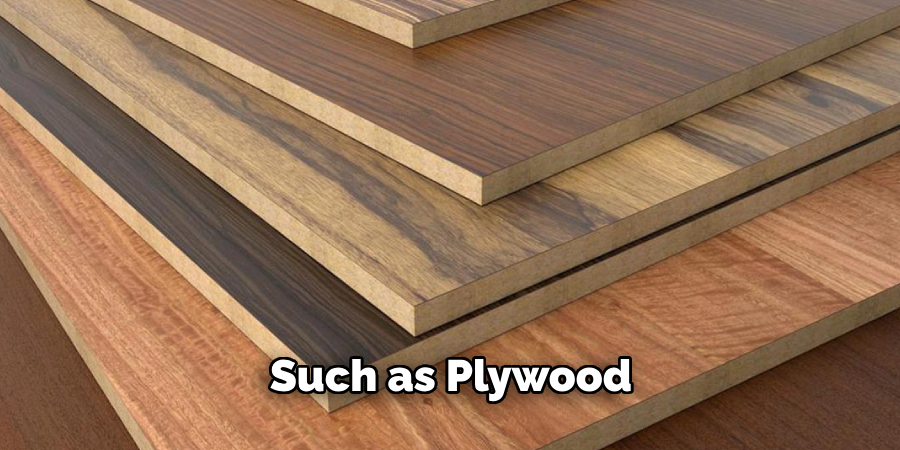
Melamine is another excellent alternative, combining affordability with a smooth surface that reduces resin adhesion. Each material has its pros and cons, so choosing the one that best fits your project requirements and budget is essential.
Creating a Blueprint
Creating a detailed blueprint is a fundamental step in planning your resin table mold. Start by sketching the desired shape and dimensions, ensuring that every aspect is meticulously measured to maintain accuracy.
This plan should include side views showing the height and thickness of the mold walls, as well as any compartments or dividers if you’re incorporating multiple resins, pours, or sections.
Precision in this stage can save you considerable time and effort during the assembly and pouring phases. By having a clear and well-thought-out blueprint, you set a strong foundation for constructing a mold that meets your design aspirations and ensures a seamless creation process.
Preparing the Mold Materials
Choosing Mold Material
When preparing to make a resin table mold, selecting the appropriate mold material is paramount to ensuring a smooth process and a quality end result. Here are the pros and cons of the most common mold materials:
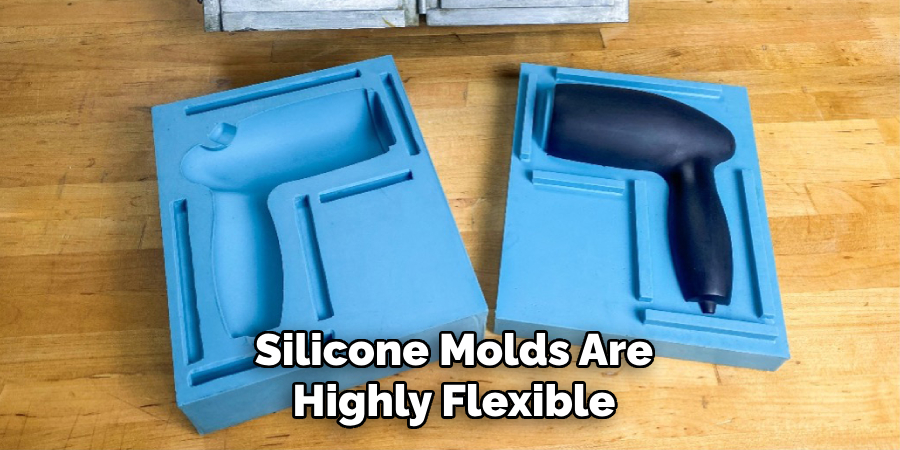
- Silicone:
- Pros: Silicone molds are highly flexible, easy to de-mold, and provide a smooth finish. They are also reusable and perfect for intricate designs due to their ability to capture fine details.
- Cons: Silicone can be quite expensive compared to other materials and may not be cost-effective for larger projects.
- Wood (e.g., Plywood or MDF):
- Pros: Wood is sturdy, relatively inexpensive, and simple to work with. It can be easily cut into custom shapes and sizes, offering great versatility.
- Cons: Wood needs to be sealed properly to prevent resin from sticking or leaking. Unsealed wood can absorb resin, compromising the mold and the project. Additionally, demolding can be more challenging than with silicone.
- Melamine:
- Pros: Melamine is affordable and has a smooth surface that reduces resin adhesion. It is also durable and can be easily cut and assembled.
- Cons: While better than wood, it still requires some release agent to ensure easy demolding and prevent resin from sticking.
Cutting and Shaping
Following the material selection, the next step involves cutting and shaping the mold material to match your detailed blueprint. Here’s a step-by-step guide:
- Gather Tools and Materials: Ensure you have all the necessary cutting tools, such as a saw for wood or melamine and a utility knife for silicone. A measuring tape, square ruler, and pencil will aid in accurate marking.
- Mark the Cutting Lines: Using your blueprint as a reference, measure and mark the dimensions on your mold material. Make sure to mark all sides and walls of the mold, including any compartments for complex designs.
- Cut the Material: Carefully cut along the marked lines. For straight, clean cuts on wood or melamine, use a table or circular saw. For silicone sheets, a sharp utility knife works best.
- Assemble the Pieces: Once all pieces are cut, assemble the mold walls using 90-degree corner clamps to ensure right angles. Secure the joints with screws or brackets for wood or melamine molds. Silicone molds may require adhesive to join the sides.
Sealing the Mold
Properly sealing your mold is crucial to preventing the resin from sticking and ensuring a smooth finish. Here’s how to do it:
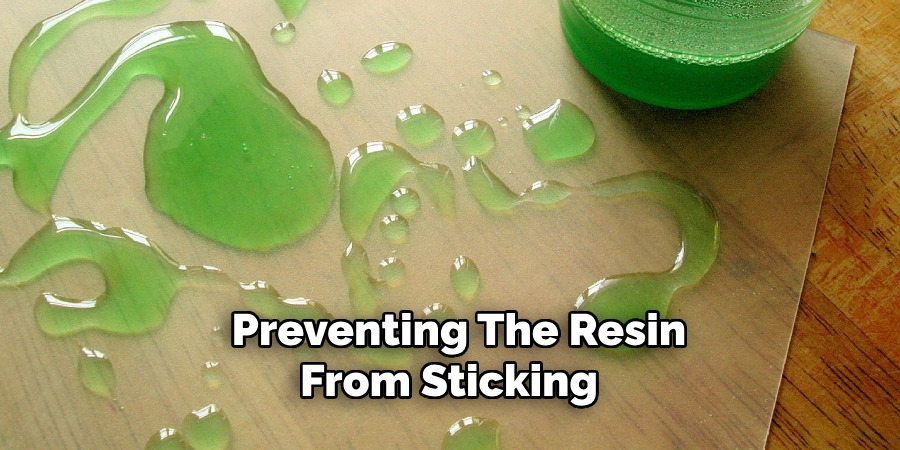
- Prepare the Sealant or Release Agent: Prepare the appropriate sealant depending on your material choice. Wood and melamine molds generally require a liquid sealant or PVA release agent, while silicone may not need additional agents due to its non-stick properties.
- Apply the Sealant: For wood and melamine, use a brush or roller to apply a layer of liquid sealant to all interior surfaces of the mold. Make sure to cover every nook and cranny, including joints and corners. Allow the sealant to dry according to the manufacturer’s instructions. If using a PVA release agent, apply it generously with a sponge or cloth.
- Reapply If Necessary: You might need to apply multiple coats depending on the sealant type and material used. Make sure each coat is fully dried before proceeding to the next.
- Test the Seal: Before pouring your resin, conduct a test with a small volume to ensure there are no leaks and the resin releases easily.
You set a solid foundation for creating stunning resin tables with professional-quality finishes by carefully choosing, cutting, and sealing your mold materials.
How to Make a Resin Table Mold: Assembling the Mold
1. Building the Base
Constructing the base of the mold is a crucial step to support the resin pour and ensure the stability of the entire structure. Begin by selecting a sturdy and flat piece of material, such as plywood or melamine, for the base. Precision in cutting and assembling the base will help prevent any warping or unevenness that could affect the final product.
- Cut the Base Piece: Measure and cut the material according to the dimensions outlined in your blueprint. Ensure the edges are smooth and straight.
- Reinforce with Bracing: To prevent any sagging or bowing under the weight of the resin, reinforce the base with support beams or bracing. This can be done by attaching wooden beams across the bottom of the base piece using screws or brackets. Position them strategically to provide maximum stability.
- Level the Base: Place the base on a flat surface and use a spirit level to check for any unevenness. Adjust accordingly to ensure a level foundation for your mold.
2. Adding Walls and Dividers
Attaching the sidewalls and any necessary dividers will create compartments within the mold, allowing for multiple sections or intricate designs in your resin table.
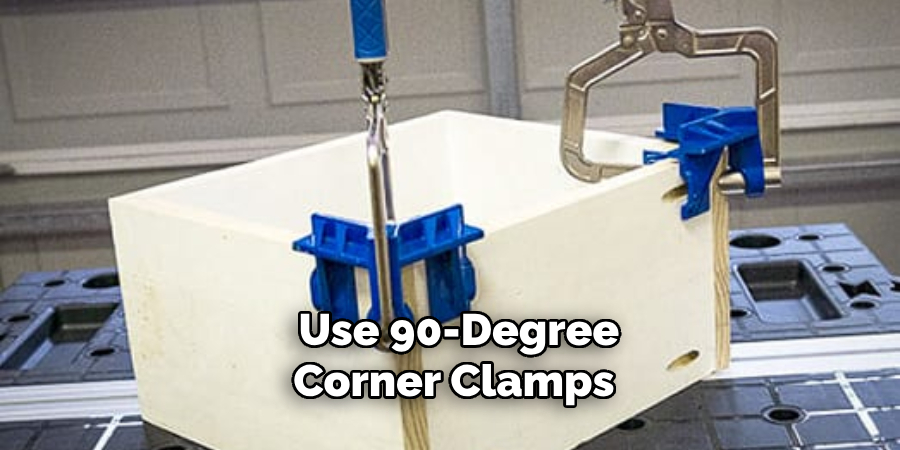
- Cut the Sidewalls: Measure and cut the sidewalls from your chosen mold material, following the dimensions in your blueprint. Make sure the walls are cut to the correct height and thickness to effectively contain the resin.
- Attach the Sidewalls: Position the sidewalls around the perimeter of the base. Use 90-degree corner clamps to hold the walls in place and ensure they are at perfect right angles. Secure the walls using screws or brackets for materials like wood and melamine. For silicone molds, use a high-strength adhesive suitable for silicone.
- Install Dividers: If your design includes multiple compartments, cut and attach the dividers as specified in your blueprint. Make sure they are firmly secured and aligned properly to prevent any resin leakage between sections.
3. Sealing Joints
Properly sealing all joints and seams is essential to prevent resin from leaking out of the mold during the pour and ensure a smooth, flawless finish.
- Prepare the Sealant: Choose a suitable sealant, such as silicone caulk, for sealing the joints. Silicone is highly effective for this purpose due to its flexibility and strong adhesion.
- Apply the Sealant: Run a bead of silicone along all the joints and seams, including where the walls meet the base and where dividers are attached. Use a caulking gun for even application and a caulk smoothing tool or your finger to smooth out the sealant, ensuring it fills all gaps.
- Allow to Cure: Let the sealant cure according to the manufacturer’s instructions. This step is crucial to ensure that the sealant sets properly and creates a watertight bond.
- Inspect the Seals: Once the sealant is fully cured, inspect all sealed areas for any gaps or weak spots. Conduct a small test pour if necessary to ensure there are no leaks.
You create a robust and leak-proof mold by meticulously building the base, attaching the sidewalls and dividers, and sealing all joints. This carefully assembled mold sets the stage for a successful resin pour and a beautifully finished resin table.
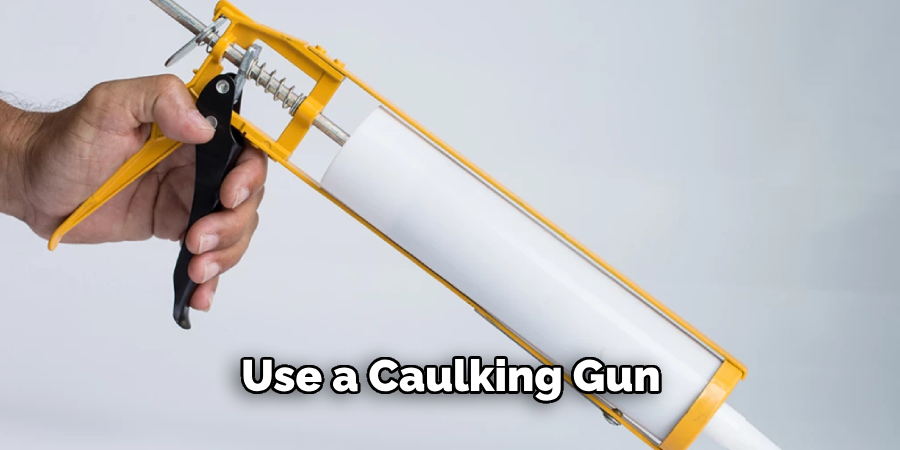
How to Make a Resin Table Mold: Preparing for Resin Pour
Surface Preparation
Before you begin the resin pour, preparing the mold’s surface meticulously is crucial. Start by thoroughly cleaning the interior surfaces of your mold to ensure there are no dust, debris, or residues that could compromise the clarity and finish of the resin. Use a microfiber cloth and a suitable cleaner to wipe down the surfaces. A mild solvent can be employed for stubborn residues, but ensure it is completely evaporated before proceeding. Once cleaned, apply a release agent.
For materials like wood and melamine, a PVA release agent is recommended. At the same time, silicone molds, typically non-stick, might still benefit from a light application to ensure a smooth demolding process. Spray or brush the release agent evenly across all surfaces and allow it to dry as per the manufacturer’s guidelines.
Positioning Inclusions
If your design incorporates inclusions such as wood pieces, flowers, or other decorative items, now is the time to arrange them within the mold. Carefully position your inclusions as per your design plan. It’s important to consider these elements’ final orientation and distribution within the resin to achieve the desired aesthetic outcome.
For heavier items, you may need to support them temporarily using adhesive or small weights to prevent them from shifting during the pour. Ensure they are firmly placed for lighter items, as they can often float when the resin is poured. Double-check the placement from different angles to ensure a balanced and visually appealing layout.
Calculating Resin Volume
Precisely calculating the resin volume needed for your project is vital to avoid shortages or excess. Begin by measuring the internal dimensions of the mold – length, width, and depth. Using these measurements, calculate the volume in cubic inches or cubic centimeters. The basic formula for calculating the volume of a rectangular mold is:
“`
Volume = Length × Width × Depth
“`
Once you have the volume in cubic measurements, convert it to the appropriate unit for your resin, typically liters or gallons. Resin manufacturers often provide coverage guidelines that can be used to determine the required volume.
Additionally, consider the volume displacement caused by inclusions—subtract the combined volume of any large inclusions from the total mold volume to get an accurate estimate. Keeping a small surplus of resin on hand is advisable to account for any slight miscalculations or unexpected needs during the pour.
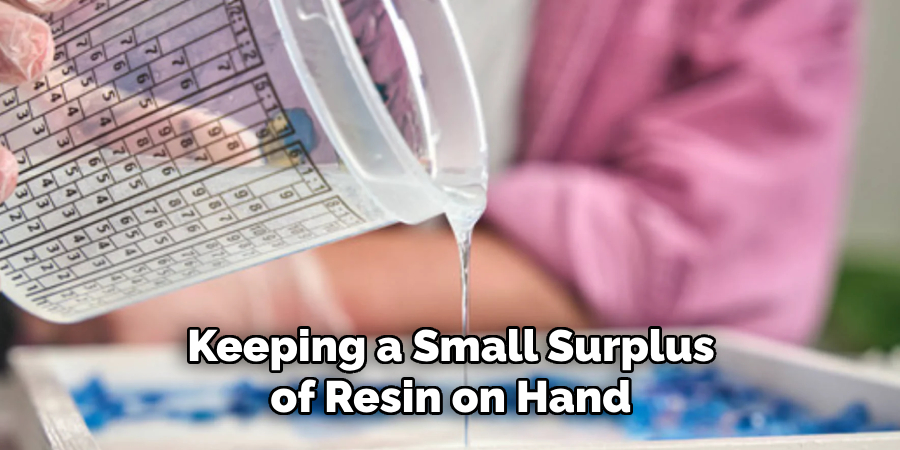
By carefully preparing the surface, thoughtfully positioning inclusions, and precisely calculating the resin volume, you set the stage for a successful and well-executed resin pour, ensuring your project runs smoothly and achieves the desired result.
Pouring and Curing Resin
Mixing Resin
Proper mixing of resin is critical to achieving a crystal-clear, bubble-free finish. Begin by reading the manufacturer’s instructions to determine the correct resin-to-hardener ratio, as different brands and types of resin may vary. Use precise measuring tools, such as graduated cups, to measure the resin and hardener components accurately. Pour the measured components into a clean mixing container.
Stir the mixture slowly and steadily using a flat stir stick or a mixing paddle. It is essential to scrape the sides and bottom of the container frequently to ensure all components are thoroughly integrated. Continue stirring for the time recommended by the manufacturer, usually between 3 to 5 minutes, until the mixture is completely homogeneous. Avoid stirring too quickly, as this can introduce air bubbles into the resin.
Pouring Resin
Once thoroughly mixed resin, it is time to pour it into the prepared mold. Begin pouring the resin slowly and steadily, starting at one corner of the mold and allowing it to flow naturally across the surface. This method helps minimize air bubbles’ introduction and ensures even coverage. If your design involves multiple layers or colors of resin, pour each layer carefully, allowing each one to level out before adding the next.
For complex designs involving inclusions, pour in stages, gently embedding and adjusting the inclusions as you proceed to achieve the desired arrangement. If air bubbles do form, use a heat source such as a heat gun or a small torch to lightly pass over the surface, popping the bubbles and creating a smooth finish.
Curing Time
Allow the resin to cure fully per the manufacturer’s instructions, typically 24 to 48 hours. The curing environment should be dust-free and stable, ideally between 70-80°F (21-27°C). Cover the mold to protect it from dust and debris during curing. Resist the temptation to move or handle the mold to avoid disturbing the curing resin.
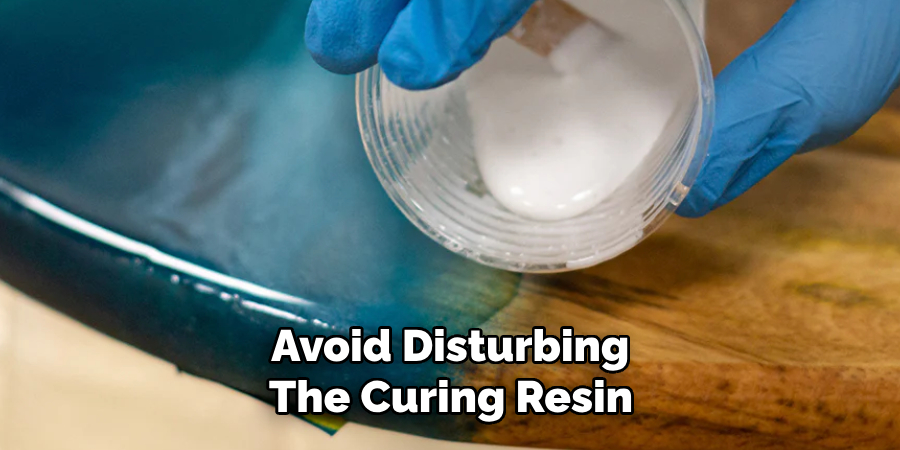
After the initial cure period, check the resin’s hardness. Some projects may require a longer cure, depending on the resin type and the thickness of the pour. Once fully cured, the resin should be hard to the touch and ready for demolding and further finishing.
By following precise mixing techniques, careful pouring methods, and appropriate curing times, you can achieve a flawless resin cast that showcases your project’s beauty and craftsmanship.
Demolding and Finishing
Demolding Process
Once the resin has fully cured, it’s time to de-mold your project. Gently start by peeling back the mold from the edges, ensuring you do not apply too much force that could damage the mold or the resin surface. If the resin seems to stick to the mold, you can use a plastic tool to carefully loosen the edges.
Avoid metal tools as they can scratch or damage the resin. Slowly and methodically work your way around the mold, coaxing the cured resin piece out bit by bit. Patience is key to avoiding any damage to your hard work.
Trimming and Sanding
After demolding, you may notice slight imperfections or excess resin that must be trimmed. Use a craft knife or a small saw to carefully trim away any drips or excess material. Once trimming is complete, sanding the edges and surfaces of your resin project is essential to achieve a smooth finish.
Begin with coarse-grit sandpaper to remove larger imperfections and gradually transition to finer grits for a polished appearance. Wet sanding can be particularly effective with resin, as it helps prevent dust and clogging of the sandpaper. Make sure to sand evenly to avoid creating flat spots or altering the shape of your project.
Applying Finish
A finishing coat can be applied to enhance the appearance and durability of your resin project. You could use a clear epoxy resin coat, a polyurethane finish, or a specialized resin polish depending on the desired outcome. Apply the finish in thin, even layers using a soft brush or a cloth, and allow each layer to dry thoroughly before applying the next.
For a high-gloss appearance, additional polishing may be required. Use a buffing wheel or a soft cloth with a polishing compound to achieve a clear, glass-like finish. This optional step can significantly enhance your resin creation’s visual appeal and longevity, giving it a professional, well-crafted look.
Conclusion
Making a resin table mold involves several essential steps and considerations. Each aspect is crucial for achieving a successful project, from selecting the right materials and ensuring proper ventilation to using the appropriate tools and adopting safety practices. We’ve detailed how to mix the resin, prevent air bubbles, and avoid leaks, providing you with a comprehensive guide on how to make a resin table mold.
Embarking on your resin casting journey opens up endless opportunities to explore your creativity. Don’t be intimidated by the process; remember, each project is a learning experience that brings you closer to mastering the art of resin casting.
Always follow safety precautions, work in a well-ventilated area, and practice patience for excellent results. Experiment with small batches and keep notes of your methods. Enjoy every step of creating your custom resin furniture, and watch as your skills and artistry evolve.
About the Author
Adrian Green, a lifelong woodworking enthusiast, shares his passion for the craft through The Woodenify Blog. With a foundation built on years of hands-on experience in his father’s woodworking shop, Adrian is dedicated to helping others learn and grow in the world of DIY woodworking. His approach to woodworking combines creativity, practicality, and a deep appreciation for the art of building with your own hands. Through his blog, he inspires individuals of all skill levels to embark on their own woodworking journeys, creating beautiful, functional pieces of furniture and décor.
Professional Focus
- Specializes in DIY woodworking projects, from furniture to home décor.
- Provides step-by-step guides and practical tutorials for woodworkers of all skill levels.
- Dedicated to helping readers build confidence and skill through easy-to-follow instructions and tips.
- Passionate about fostering a community of makers who can share, learn, and grow together.
Education History
- University of Craft and Design – Bachelor of Fine Arts (BFA) in Woodworking and Furniture Design
- Woodworking Apprenticeships – Extensive hands-on training with skilled craftsmen to refine carpentry and furniture making techniques.
- Online Courses & Masterclasses – Continued education in advanced woodworking techniques, design principles, and specialized tools
Expertise:
- DIY woodworking, carpentry, furniture making, and home décor projects.
- Creating accessible tutorials and guides for beginner to advanced woodworkers.
- Sharing the joys and satisfaction of woodworking, from raw materials to finished products.